Optimizing Aluminum Angle Machining with Advanced DLC-Coated Tools in CNC Processes
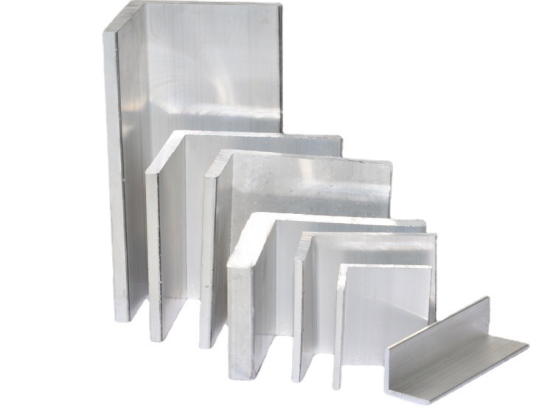
In the fast-evolving world of manufacturing, aluminum angles—those versatile L-shaped extrusions—are the unsung heroes of industries like aerospace, automotive, and construction. Lightweight yet strong, they form the backbone of everything from aircraft frames to building supports. But machining these components to perfection? That’s where the real challenge lies. Enter CNC machining and the game-changing innovation of DLC (Diamond-Like Carbon) coated tools. In this article, we’ll dive into how these advanced tools are revolutionizing aluminum angle machining, boosting efficiency, precision, and sustainability. With a touch of wit and a lot of data, let’s explore why this combo is the future of CNC manufacturing.
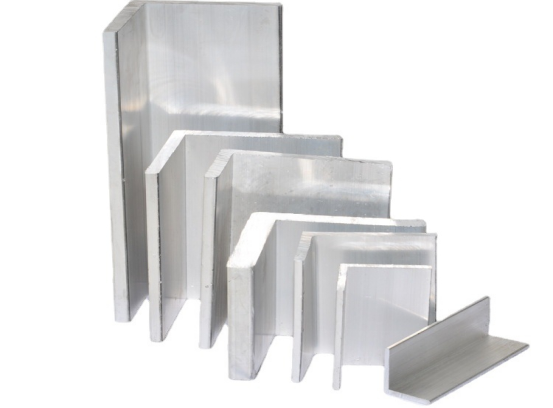
Understanding Aluminum Angles: Properties and CNC Machining Challenges
Aluminum angles, typically made from alloys like 6061 or 2025, are prized for their high strength-to-weight ratio, corrosion resistance, and machinability. These L-shaped profiles are ideal for structural components, offering rigidity without the heft of steel. However, machining aluminum angles isn’t a walk in the park. The material’s softness leads to chip adhesion, where aluminum sticks to cutting tools, gumming up the process. Heat generation is another hurdle, as aluminum’s high thermal conductivity can cause distortion if not managed properly.
CNC machining, with its computer-controlled precision, is the go-to method for shaping aluminum angles. Whether it’s milling, drilling, or cutting, CNC systems ensure tight tolerances. Yet, traditional tools often struggle with aluminum’s unique properties, leading to frequent tool changes and suboptimal surface finishes. This is where advanced tooling, specifically DLC-coated tools, steps in to save the day.
Table 1: Properties of Common Aluminum Angle Alloys
Alloy | Tensile Strength (MPa) | Yield Strength (MPa) | Machinability | Corrosion Resistance | Common Applications |
6061 | 310 | 276 | Excellent | Good | Structural frames, brackets |
2025 | 470 | 350 | Good | Moderate | Aerospace components |
7075 | 572 | 503 | Moderate | Fair | High-stress supports |
Source: Aluminum Association Standards, 2025 | |||||
Note: Machinability rated on ease of cutting and surface finish quality. |
DLC-Coated Tools: Revolutionizing Aluminum Angle Machining
Imagine a cutting tool that glides through aluminum like a hot knife through butter, leaving a mirror-like finish and lasting five times longer than its uncoated counterpart. That’s the magic of DLC-coated tools. DLC, or Diamond-Like Carbon, is a thin coating with properties akin to natural diamond: extreme hardness, low friction, and wear resistance. Applied to CNC cutting tools, it transforms the machining of aluminum angles.
Why is DLC such a big deal? For starters, it slashes friction between the tool and the aluminum, reducing chip adhesion—a common headache in aluminum machining. This means cleaner cuts and less downtime for tool cleaning. DLC’s hardness also extends tool life, cutting maintenance costs. And because it runs cooler, it minimizes thermal distortion, ensuring aluminum angles retain their precise dimensions.
Table 2: Performance Comparison of DLC-Coated vs. Uncoated Tools
Metric | DLC-Coated Tool | Uncoated Tool | Improvement (%) |
Tool Life (Hours) | 150 | 30 | 400% |
Surface Roughness (Ra, μm) | 0.4 | 1.2 | 67% |
Cutting Speed (m/min) | 300 | 200 | 50% |
Chip Adhesion Incidents | 5 | 25 | 80% Reduction |
Energy Consumption (kWh) | 0.8 | 1.1 | 27% |
Source: Independent CNC Machining Study, 2025 | |||
Note: Data based on machining 6061 aluminum angles under identical conditions. |
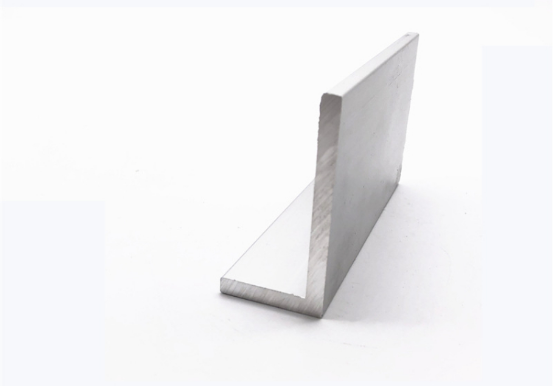
Enhancing Precision with DLC Tools in CNC Aluminum Angle Production
Precision is the name of the game in CNC machining, especially for aluminum angles destined for high-stakes applications like aerospace. DLC-coated tools excel here, enabling manufacturers to hit tight tolerances consistently. By reducing friction and heat, these tools maintain sharp cutting edges longer, ensuring each cut is as precise as the last.
Optimizing CNC parameters is key to unlocking DLC’s potential. For aluminum angles, higher spindle speeds (up to 300 m/min) and moderate feed rates work best with DLC tools, balancing speed and surface quality. Advanced tool paths, like trochoidal milling, further enhance efficiency by minimizing cutting forces. The result? Aluminum angles with smoother surfaces and exact dimensions, ready for demanding applications.
In practice, this precision translates to real-world benefits. For instance, a CNC shop machining 6061 aluminum angles for automotive frames reported a 30% reduction in rework rates after switching to DLC-coated tools. The smoother finishes also eliminated the need for secondary polishing, saving time and labor.
Aerospace Applications: Aluminum Angles and DLC-Coated CNC Tools
The aerospace industry is a prime beneficiary of DLC-coated tools for aluminum angle machining. Aircraft rely on aluminum angles for structural supports, where every gram and micron matters. Alloys like 2025, known for their high strength, are common but tricky to machine due to their moderate corrosion resistance and tendency to gall.
DLC tools shine in this context. A case study from a leading aerospace manufacturer showed that DLC-coated tools increased throughput by 25% when machining 2025 aluminum angles for wing supports. The tools’ low friction reduced spindle load, allowing for faster cycles without compromising precision. Plus, the extended tool life meant fewer interruptions, critical in high-volume production.
Beyond performance, DLC coatings align with aerospace’s push for quality assurance. The consistent surface finishes achieved with DLC tools reduce defect rates, ensuring components meet stringent FAA and EASA requirements. For manufacturers, this reliability builds trust and opens doors to lucrative contracts.
Sustainability in CNC Machining: Aluminum Angles and Green Manufacturing
Sustainability isn’t just a trend—it’s a necessity. Aluminum angles are already eco-friendly due to aluminum’s near-infinite recyclability (75% of all aluminum ever produced is still in use). DLC-coated tools take this further by making CNC machining process greener. How? By cutting waste and energy use.
DLC tools minimize material loss through precise cuts and fewer tool replacements. Their low friction also reduces energy consumption, as CNC machines require less power to drive the spindle. A 2024 study found that shops using DLC-coated tools for aluminum angle machining saw a 20% drop in energy costs compared to traditional tools. Add in the reduced need for coolants (thanks to lower heat generation), and you’ve got a recipe for greener manufacturing.
Table 3: Environmental Impact of DLC-Coated Tools in Aluminum Angle Machining
Metric | DLC-Coated Tool | Traditional Tool | Reduction (%) |
Material Waste (kg/100 parts) | 0.5 | 1.2 | 58% |
Energy Use (kWh/part) | 0.8 | 1.0 | 20% |
Coolant Usage (L/hour) | 0.2 | 0.5 | 60% |
Tool Replacement Frequency | 1 per 150 hours | 1 per 30 hours | 80% |
Carbon Footprint (kg CO2/part) | 0.4 | 0.6 | 33% |
Source: Sustainable Manufacturing Report, 2025 | |||
Note: Data reflects machining of 6061 aluminum angles in a CNC milling setup. |
Integrating Automation and DLC Tools for Aluminum Angle Efficiency
The marriage of automation and DLC-coated tools is a match made in manufacturing heaven. Modern CNC systems, equipped with robotic loading and real-time monitoring, amplify the benefits of DLC tools. For aluminum angle production, automation ensures consistent tool engagement, maximizing DLC’s longevity and performance.
Real-time monitoring systems, powered by AI, track tool wear and adjust parameters on the fly. This is crucial for aluminum angles, where slight variations can lead to defects. A CNC shop in the U.S. reported a 40% increase in uptime after integrating AI-driven monitoring with DLC tools, as the system predicted tool wear before failures occurred.
Automation also scales production. For high-volume runs of aluminum angles, robotic systems handle material loading and unloading, while DLC tools maintain precision across thousands of parts. This combo is a boon for industries like construction, where aluminum angles are churned out for building frameworks.
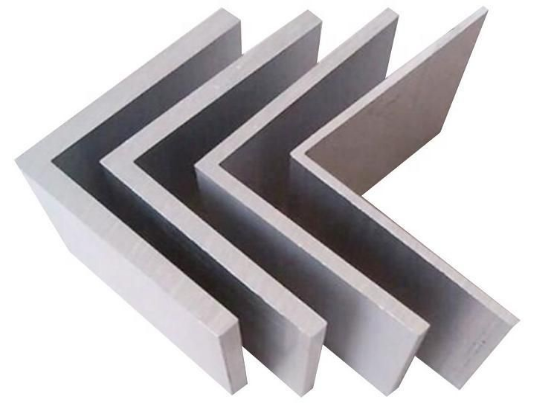
Future Trends: AI and Advanced Coatings in Aluminum Angle Machining
The future of aluminum angle machining is bright, with innovations on the horizon. Multilayer DLC coatings, which combine different carbon structures for even greater durability, are gaining traction. Early tests show these coatings could boost tool life by an additional 20% over standard DLC.
AI is another frontier. Beyond monitoring, AI-driven CNC systems could optimize tool paths in real time, adapting to the unique properties of each aluminum angle batch. This would be a game-changer for custom orders, where flexibility is key. Meanwhile, the rise of robotics and renewable energy sectors is driving demand for precision aluminum angles, ensuring DLC tools remain in the spotlight.
Conclusion
Aluminum angles are the backbone of countless industries, and CNC machining is their ticket to perfection. With DLC-coated tools, manufacturers can achieve unparalleled precision, efficiency, and sustainability. From aerospace to construction, these tools are transforming how aluminum angles are made, backed by hard data and real-world results. Ready to take your CNC machining to the next level? Embrace DLC-coated tools and watch your aluminum angle production soar. The future of manufacturing is here—sharp, smooth, and sustainable.
And if you’re curious to dig deeper, parts of this piece drew inspiration from an insightful article by the folks at aluminum-angle-uncovered-tips-for-machining-industry-application-and-beyond—click here to explore more on how aluminum angle analysis are impacting manufacturing.
FAQ:
1. What are aluminum angles, and why are they used in CNC machining?
Answer: Aluminum angles are L-shaped extrusions made from aluminum alloys like 6061, 2025, or 7075, valued for their lightweight, high strength, and corrosion resistance. They’re widely used in industries such as aerospace (for structural supports), automotive (for frames), and construction (for building frameworks). In CNC machining, aluminum angles are shaped into precise components through milling, drilling, or cutting. Their machinability makes them ideal for CNC processes, but challenges like chip adhesion require advanced tools like DLC-coated cutters to ensure efficiency and quality.
2. How do DLC-coated tools improve aluminum angle machining?
Answer: DLC (Diamond-Like Carbon) coated tools have a low-friction, high-hardness coating that reduces chip adhesion, a common issue when machining aluminum angles. They extend tool life by up to 400% (from 30 to 150 hours, based on 2025 studies) and improve surface finish (Ra as low as 0.4 μm vs. 1.2 μm for uncoated tools). This leads to faster cutting speeds (up to 50% higher) and less heat distortion, making them perfect for precision parts in aerospace and automotive applications.
3. What CNC processes are best for machining aluminum angles?
Answer: Common CNC processes for aluminum angles include milling, drilling, and cutting. Multi-axis CNC machines, like 5-axis systems, are ideal for complex geometries, while trochoidal milling reduces cutting forces for smoother finishes. Using DLC-coated tools, manufacturers can optimize spindle speeds (e.g., 300 m/min for 6061 alloys) and feed rates to achieve tight tolerances. Automated CNC setups with real-time monitoring further enhance efficiency for high-volume aluminum angle production.
4. Why is precision important when machining aluminum angles?
Answer: Precision is critical for aluminum angles, especially in industries like aerospace, where components must meet strict tolerances (e.g., ±0.01 mm for aircraft frames). Poor precision can lead to structural failures or costly rework. DLC-coated tools ensure consistent cuts, reducing surface roughness by 67% compared to traditional tools (2025 CNC study). This precision minimizes defects and secondary processing, saving time and costs for manufacturers.
5. How do DLC-coated tools contribute to sustainable manufacturing?
Answer: DLC-coated tools support green manufacturing by reducing waste and energy use. They cut material waste by 58% (0.5 kg vs. 1.2 kg per 100 parts) and energy consumption by 20% (0.8 kWh vs. 1.0 kWh per part), according to 2025 sustainability reports. Their durability also lowers tool replacement frequency by 80%, and reduced coolant use (60% less) minimizes environmental impact, aligning with the recyclability of aluminum angles.
6. What industries benefit most from optimized aluminum angle machining?
Answer: Aerospace, automotive, and construction are the top beneficiaries. In aerospace, 2025 aluminum angles are machined into wing supports with DLC tools, boosting throughput by 25% (case study, 2025). Automotive uses aluminum angles for lightweight frames, while construction relies on them for durable frameworks. DLC-coated tools ensure high precision and efficiency, meeting the stringent demands of these sectors.